- Equipment
- P325E-FI
P325E-FI
P325E-FI
Details
P325E-FI Benefits:
- Precision engineered components housed in a stainless steel fabrication
- 24/7 production capability
- Servo drive to the infeed, seam crimp rollers and end crimp
- Easily adjustable for collations of 4, 6, 8 and 10 apples
- 50 product settings that automatically change the bag length, print registration, end crimp slow down, in feed position, machine speed, and printed code and label position
- 70 packs per min. based on a 6-pack configuration
- Cantilever design to enhance hygienic cleaning and improve maintenance access
- Collation multi conveyor assembly at delta plate area
- Seam crimp release to prevent film melt when the machine stops
- One overhead with soft rubber paddles to support and retain the apple collations through the seam crimp module for all pack collations
- Rotary end crimp with jaw centers to suit product requirement and knife and anvil with fine adjustment for parallelism
- Carryover conveyor
- Precision temperature controllers for the seam crimp and end crimp heaters
- Sealed seam crimp and end crimp slip rings
- End crimp timed stop to prevent film melt when the machine is stationary
- Perforated steel end crimp guarding with gas spring support for operator safety
- Long product out-feed conveyor
Works With
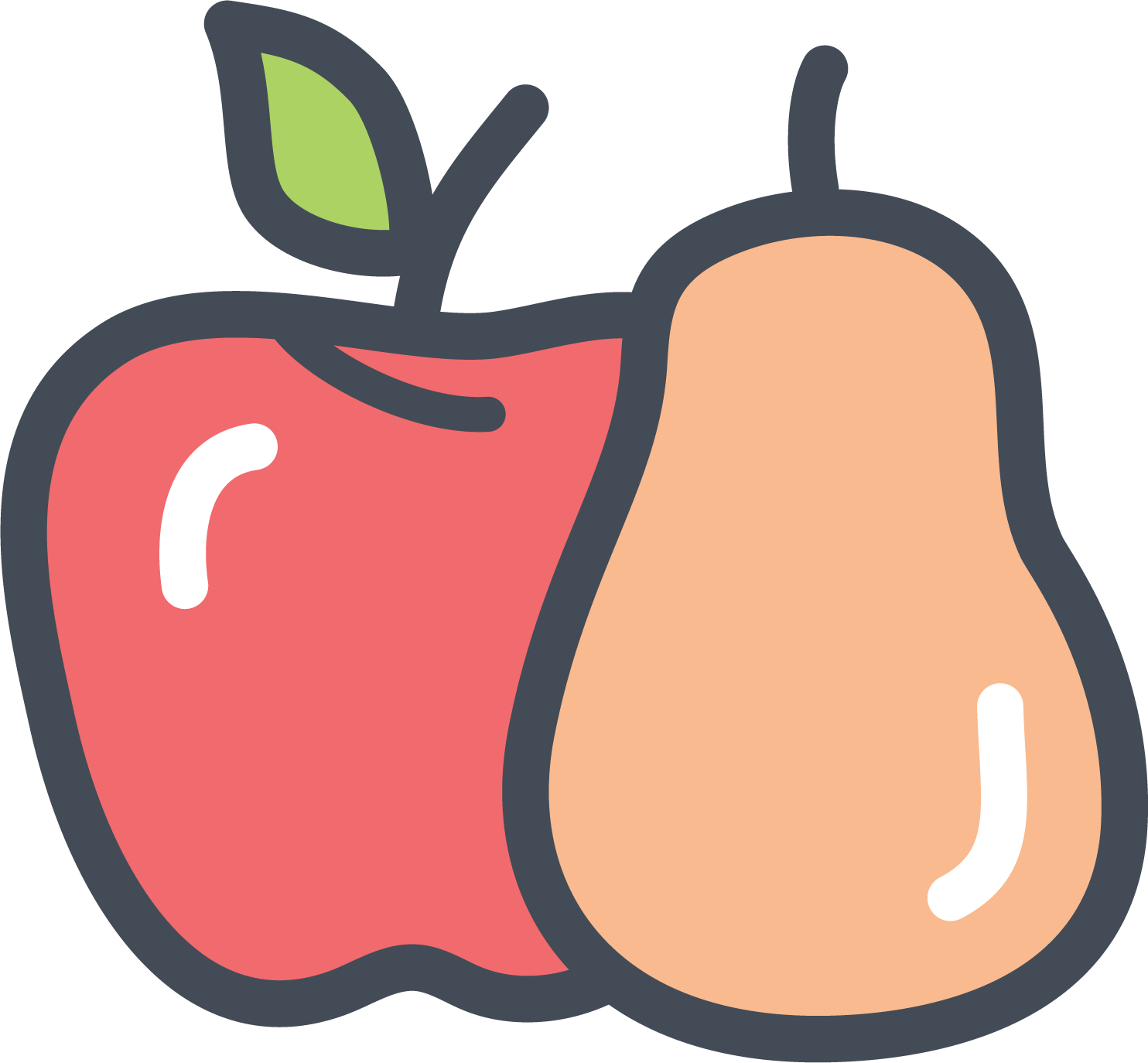
Details
P325E-FI Benefits:
- Precision engineered components housed in a stainless steel fabrication
- 24/7 production capability
- Servo drive to the infeed, seam crimp rollers and end crimp
- Easily adjustable for collations of 4, 6, 8 and 10 apples
- 50 product settings that automatically change the bag length, print registration, end crimp slow down, in feed position, machine speed, and printed code and label position
- 70 packs per min. based on a 6-pack configuration
- Cantilever design to enhance hygienic cleaning and improve maintenance access
- Collation multi conveyor assembly at delta plate area
- Seam crimp release to prevent film melt when the machine stops
- One overhead with soft rubber paddles to support and retain the apple collations through the seam crimp module for all pack collations
- Rotary end crimp with jaw centers to suit product requirement and knife and anvil with fine adjustment for parallelism
- Carryover conveyor
- Precision temperature controllers for the seam crimp and end crimp heaters
- Sealed seam crimp and end crimp slip rings
- End crimp timed stop to prevent film melt when the machine is stationary
- Perforated steel end crimp guarding with gas spring support for operator safety
- Long product out-feed conveyor
Downloads
Technical Specs
Electrical requirement
380/440v 50HZ 3Ph N+Earth
Electrical consumption
n 7kVA (16 amps per phase max)
Pneumatic requirement
6Bar minimum dry clean air supply
Wrapping materials
Generally OPP
Apple collations
4-6-8-10 (arranged in soldier format)
Product height (mm)
To suit
Product width (mm)
To suit
Product length (mm)
To suit
Reel diameter (mm)
300 (max)
Core diameter (mm)
75
Width (mm)
650 (max)
Machine speed (ppm)
70 (based on a 6 pack formation)
Noise emission
Less than 70dba at 1m distance,
1.6m above floor
Approx. wt. (kg)
1000
Approx. size (mm)
1730 H x 1030 W x 5580 L
(with standard 3.5 metre long infeed)
About Company
Redpack Packaging Machinery designs and manufactures Flow Wrapping and Packaging Machinery. Our markets include industries such as fresh produce, pharmaceuticals, snack foods, household products, bakery, greeting cards, gifts and toys, etc. With a brand stretching back over 35 years our flow wrapping design follows tried and tested techniques. Despite this each application brings its own unique requirements for custom designed features.
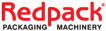